The mechanisms of cement additives
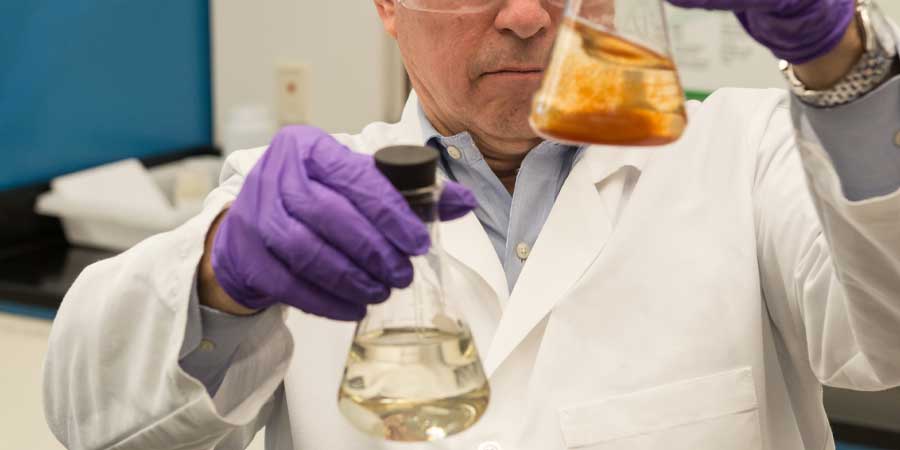
The mechanisms of cement additives
Cement additives enhance the efficiency of the grinding process. The cement treated with these additives has a narrower particle size distribution (PSD). This narrower PSD impacts cement performance characteristics, including paste water demand, setting time, and strength development. More significantly, many cement additives include wide ranging chemical components designed to influence cement hydration and thereby further improve the cement performance characteristics by chemical activation.
The type and magnitude of these influences depends on many factors, such as additive type dosage, application, mill system design and operation, cement characteristics, and more.
Although there are many factors that influence the water demand, setting time, and strength development, the chart below provides an indication of the range of changes that are possible with different cement additives.
Examples of cement additive components
There are numerous types of additives for improving cement performance and these can contain combinations of both organic and inorganic compounds. For example:
- Triethanolamine or higher alkanolamine-based additives support more efficient grinding and enhanced cement hydration. In some cases, they catalyze the C3S hydration reaction to produce earlier initial set and strength.
- Cement additives with retarding properties improve the flow and set properties of cement.
- Na/Ca chlorides and Na acetate/formate are helpful for increasing early strength of cement.
- Polymer-based additives can contribute to the fluidity of the mix.
Uses of alkanolamines
There are several alkanolamines that exhibit both excellent grinding aid properties as well as hydration enhancing properties. The most widely used higher alkanolamine, tri-isopropanolamine, accelerates the hydration of the interstitial phases similar to triethanolamine. However, unlike triethanolamine, tri-isopropanolamine remains active in the solution for several days, and has a strong impact on the solubility of ferrite and iron-rich hydrates, preventing them from blocking the surface of alite and belite.
The iron-solubilizing effect of tri-isopropanolamine over time has a strong strength enhancing effect at 28 days, with a stronger effect for coarse, iron-rich cements. The strength enhancing effect of tri-isopropanolamine is therefore less pronounced for cements with high fineness (less blocking effect of the ferrite phase) and low iron content.
Tri-isopropanolamine is especially powerful as a strength-enhancing additive for limestone cements. It reduces the porosity and improves the cement strength by incorporating calcium carbonate into the structure of the cementitious binder.
Conclusion
Cement additives have a positive influence on cement performance characteristics by design. Dry dispersion provides enhanced grinding efficiency and narrower PSD. Selection of certain chemical components ensures the appropriate effect on cement hydration, often combining acceleration and retarding properties, to achieve the desired effect on water demand, setting and strength development.
The use of cement additives requires careful consideration to ensure appropriate performance and optimum economics.
Learn more about cement additives.
Tags
- Cement additives
- Cement grinding
- Cement production
- OPTEVA™
- Producer
- Sustainability
- TAVERO™