How to Combat Coastal Concrete Corrosion
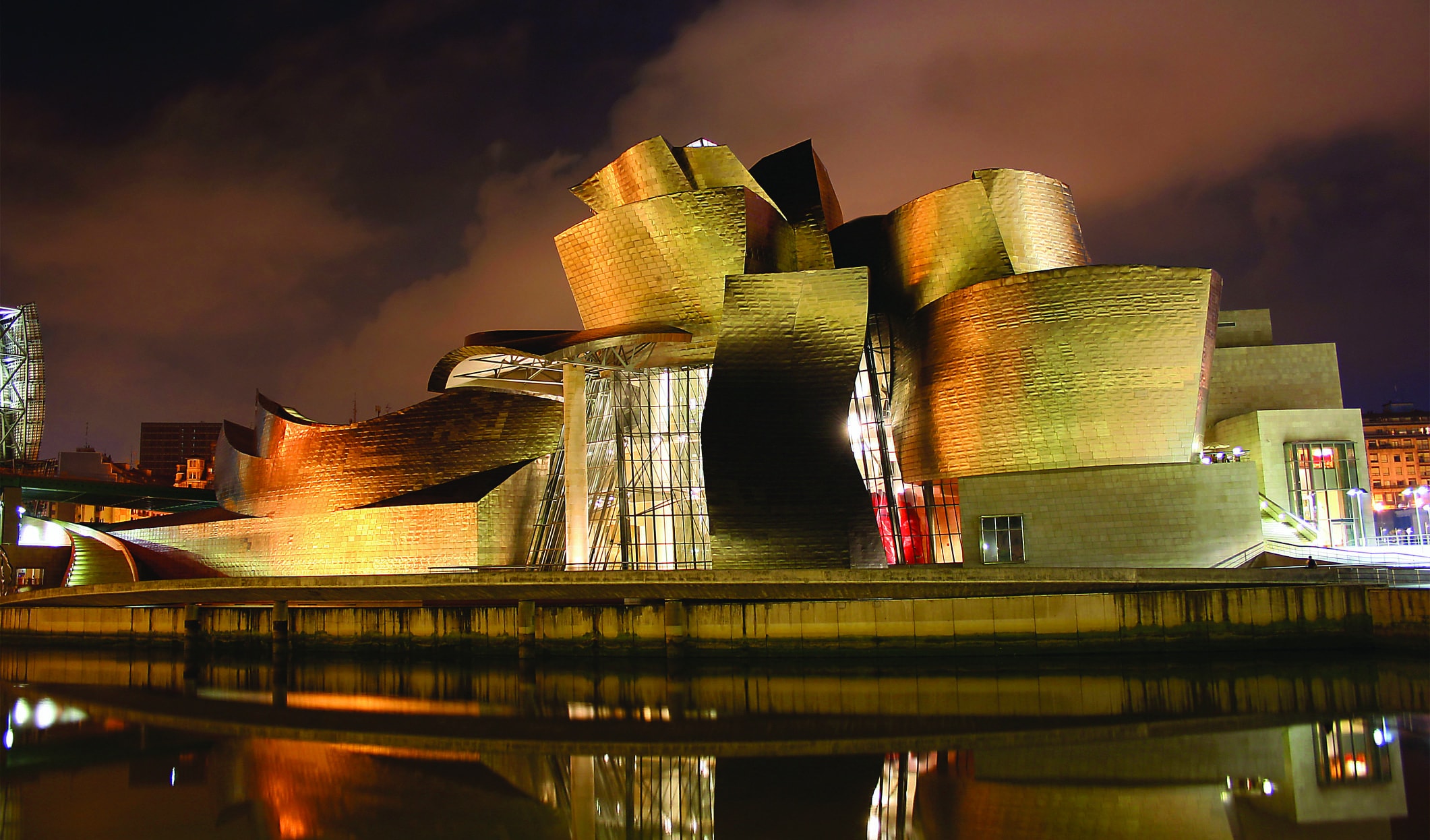
Many buildings across the world are constructed in coastal areas with below grade structures. Concrete is ideal for such construction, but can become vulnerable to the complex combination of corrosive seawater, aggressive soil conditions and a high water table.
Thankfully, proven solutions are available. GCP Applied Technologies explains how to ensure water tightness in coastal areas.
Compromised concrete
In coastal locations, unprotected concrete and steel reinforcement are severely compromised by seawater sulphates and chlorides, the effects of which can lead to long-term corrosion, leaks and compromised durability of the entire structure.
Seawater includes a complex cocktail of chemicals which can cause steel reinforcement to corrode and expand, forcing the concrete to crack and fracture. The cracks compound the problem by providing further paths for contamination to enter. No matter how small these penetrations, the concrete is jeopardised, leading to a potentially dramatic reduction in its service life.
The problem is worse in hotter countries, with every 10°C-increase doubling the rate of corrosion.
The solution: A barrier
While continuous advancements in concrete production have improved resistance to aggressive ground conditions, a waterproofing barrier which completely prevents infiltration is the only way to preserve its structural integrity. The ideal solution is an impermeable barrier membrane, which also stops water migration occurring between the membrane and the building itself.
Water migration causes considerable headaches in locating leaks in conventional membranes. When a leak becomes visible, it is often some distance from the source, making locating and fixing leaks haphazard and expensive. It makes the whole structure vulnerable. Some membranes are mechanically attached to concrete using a fleece-like interface that separates the waterproofing membrane from the structure. This method inherently provides pathways for water to enter and migrate.
PREPRUFE® is the proven solution
GCP Applied Technologies' PREPRUFE® waterproofing membrane combines synthetic adhesive layers with a robust HDPE film to provide a permanent waterproofing barrier unaffected by seawater, even if chemical concentration changes over time.
PREPRUFE®'s ADVANCED BOND TECHNOLOGY™ prevents water ingress by intimately adhering the membrane to concrete, forming a continuous impenetrable seal between the membrane and structure. Unlike mechanically attached bonding systems, PREPRUFE® protects the structure from water migration via capillary action common in mechanically attached bonding systems. An additional benefit of PREPRUFE® is its flexibility around complex details, minimising application time and project cost overruns.
With the impact of failure of below grade waterproofing and increased application times leading to significant costs, choosing the right waterproofing membrane and bonding technology is crucial for the client and project team's success. PREPRUFE® has been proven to have a service life in excess of 100 years bringing peace of mind during a project and long after its completion.
For more about the full range of PREPRUFE® products visit preprufe.com or for general enquiries, including technical and on- or off-site support, please contact preprufe@gcpat.com.
Tags
- Commercial buildings
- Concrete
- PREPRUFE®
- Waterproofing