Admixtures and sustainability
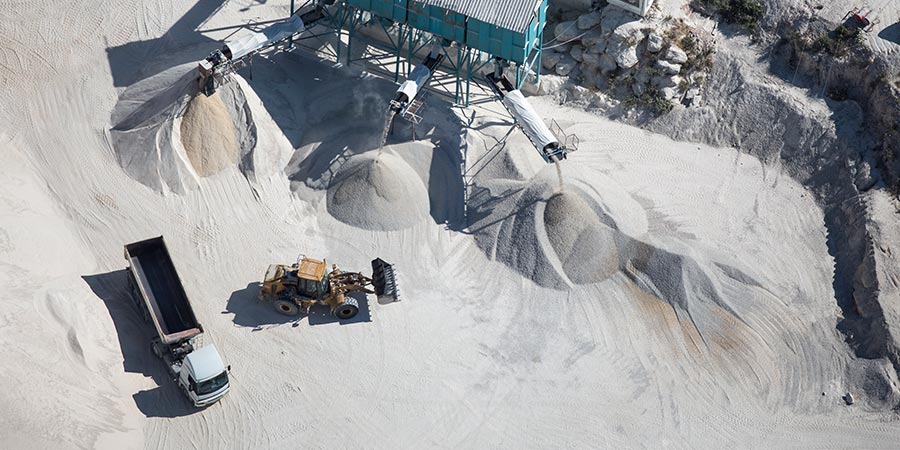
Cement additives and concrete admixtures are construction chemicals that reliably improve the sustainability of a broad range of cement-based systems. This improvement can be derived from enhancing durability and strength through water reduction, and catalyzing the cement hydration process to enable replacement of clinker with supplementary cementitious materials.
Today, different admixture technologies are often used in combination, especially in concrete systems that incorporate secondary cementitious materials (SCMs), where not only water reduction but also chemistries that catalyze the cement hydration reaction are used to allow for more inclusion of SCMs while maintaining the specified strength.
- Dispersant-based water reducers and superplasticizers - Dispersant-based water reducers are one of the most effective concrete enhancing technologies developed. These dispersing agents have the ability to deflocculate cement grains and other fine particles, thereby releasing the water that is otherwise bound in the cement flocs. This action leads to an increase in the bulk flow of the concrete system. Application of these powerful water reducing chemistries has enabled production of concrete with favorable rheological properties. Another way that water reducers can be employed to increase sustainability is by using less cement content or more SCMs in the concrete.
- Air entraining agents - Air entraining agents (AEAs) are surface active agents which function by stabilizing small air bubbles in the concrete to provide pressure relief when entrained water expands during freezing. For this reason, AEAs are required by building codes in many freeze-thaw susceptible regions in the world, and have been successfully used for 75 years. AEAs can also play a significant role in the reduction of CO2 derived from mortar production, an application which accounts for 40% of the cement used in the developing world or about one third of the world cement production. Through incorporation of AEAs, mortar manufacturers can achieve comparable flow, via the lubricating effect of the air bubbles, to the more common methods of adding more cement or water to the system.
- Accelerators - Set and hardening accelerators have been known and used for well over a century. Their ability to catalyze the hydration of cement and compensate for the low early strength development with SCMs make them indispensable to the production of cement-based products. They are generally soluble calcium salts of chloride, nitrate and nitrite. Other classes of accelerators include sodium thiocyanates and amines. Although very effective, chloride salts are frequently excluded from use by specification, due to their potential to encourage corrosion of reinforcement components. As a result, greater application of non-chloride and non-corrosive accelerators provides another promising alternative to enable development of sustainable concrete.
Admixture adaptation to new cementitious systems
Innovative use of cementitious materials, for example limestone calcined clay and development of new clinker are important technologies for reaching the sustainability goal for cement-based materials. To achieve maximum sustainability, their use needs to be accompanied by admixtures, particularly in cases where minimization of water usage is required.
The increase in use of various raw materials in the production of concrete, whether as cementitious materials, aggregates or admixtures, can inevitably create complex interaction effects. In the most severe cases, these negative interactions may lead to production of green concrete which will not set, or weak concrete, which has a poor microstructure and short life span. Provided that these obstacles are circumvented, sustainable concrete production (i.e., a net reduction in CO2 emissions over the life-cycle of a structure) can be achieved by (1) a reduction of cement used, (2) a reduction of mixing and/or placement energy, and (3) an increase in longevity of the concrete structure.
To make the most sustainable concrete, some of the procedures need to be tailored to the specific locations of use, and this depends on the infrastructure and the available transport capabilities to and from the job site. In locations where bulk cement is used, for example in urban ready mix concrete plants, chemicals are added in both the cement grinding and concrete mixing processes. It is, therefore, important to take all of the chemicals entering the final concrete into account. Conversely, in locations where bagged cements are typically supplied, for example in manual mixing concrete sites, the use of cement additives in their maximum dosage levels is critical to the production of high-quality concrete that incorporates a significant portion of SCMs.
Tags
- Cement additives
- OPTEVA™
- TAVERO